FAQs – Ground & Water Solutions Centre
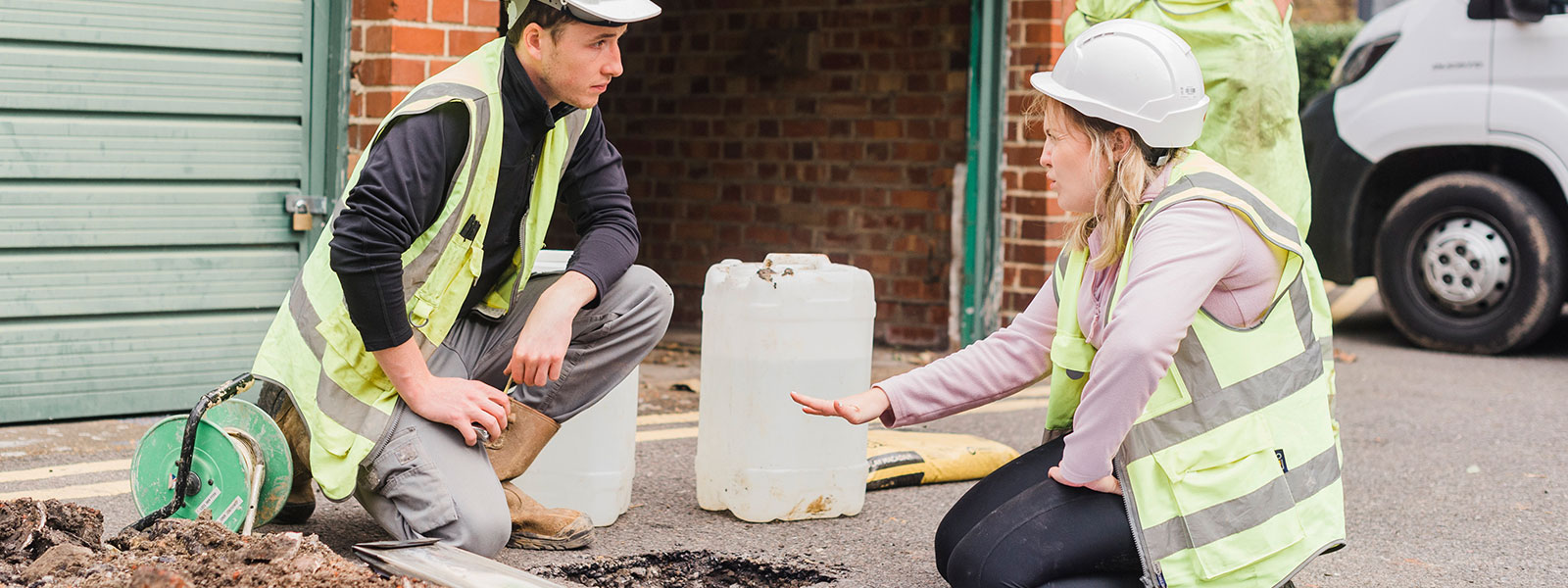
Preparatory work
Why do you keep coming back with more questions?
We suspect utilities could limit suitable areas to dig. What do you need?
Why have you raised an issue over site access?
How quick can I get my results?
Can I get an indication of the results earlier?
Of course. Post site works, we will phone you and discuss the results and their implications. You can get a written preliminary report within six working days of site works. At any point you can call the Engineer in charge and discuss your site.


Problems with boreholes / sampling
We do not understand why our previous SI was rejected?
We have been told poor class samples do not allow for engineering review of ground conditions. Why?

Value / Judgement / Competence
I have had a cheaper quote for the boreholes than your price. Why are you more expensive?
For example, in accordance with guidance, a sample derived from a Flight Auger/CFA rig is too disturbed even for general descriptive classification. Basic classification tests can only be undertaken on samples with a certain level of disturbance. This is the same for the strength tests used. Such as, Mackintosh Probes, which are only generally suitable for sensitive soils and are pointless where dense gravels are noted (e.g., in London, when undertaking a basement). Another example is SPT’s, which can be unreliable in chalk. Less reliable information may mean more conservatism in design, which may drive up construction costs unnecessarily.
Are we comparing like for like? Most of the time a price difference is due to a specification difference. Deeper/shallow boreholes, falling head instead of BRE soakage tests, no SPT’s, no UT100’s. It’s a bit of a minefield so please don’t be afraid to discuss it with us, each test has its pros and cons.
Who do you use for laboratory certification?
Are you a competent person, in accordance with the guidance?
From a more practical perspective all reports are overseen or undertaken by a Senior Engineer. Accreditations within the Company are with all major bodies that influence the industry including the Society for Brownfield Risk Assessment (SoBRA), Association of Geo-environmental and Geotechnical Specialists (AGS) and The Geological Society of London, with some members of the latter having reached Chartered Status. Influence within these bodies is maintained through working group participation.
A previous SI was not supervised. Will it be ok?
We will ensure we have experienced personnel, who know what they are looking for from a SI, on site as part of the drilling and technical team. We ensure quality information is built into our service provision from the start.
Will the reports be accepted by the Local Authority?
However, sometimes, there are internal changes in a council policy, that are not communicated to all parties. This may be a change in policy on vapour risk assessments, groundwater risk assessments, groundwater monitoring, etc. In these circumstances a little extra bit of SI may be required to push it over the line.
For a Phase 1 Desk Study, can I get away with a Site Check Report or similar?
Can I get away with just a couple of soil tests?
Less sampling and testing mean more uncertainty. If you can adequately manage that uncertainty, then great; but uncertainty can lead to conservatism and an over engineered design. So, we must always balance risk and reward. We request that you are open with us in this regard, so we can have an honest conversation about what you need.
Why are you now asking for more samples and data?
Sometimes the results are uncertain, i.e., we get a couple of positives and the rest negative. More samples mean more certainty in the data, which lead to better evidence-based decisions being made and provides reassurance when a council officer reviews the report. We mainly want to avoid one scenario, the false positive. False positives mean you remediate a site when it is not required. Sometimes more info aids this.
Why do council requirements differ so much?
The area’s specific geology and history will mean that councils will have different concerns. Therefore, a one size fits all policy may not be appropriate, so some adaptation of SI requirements may be needed in certain areas. The earlier we talk about this the better.

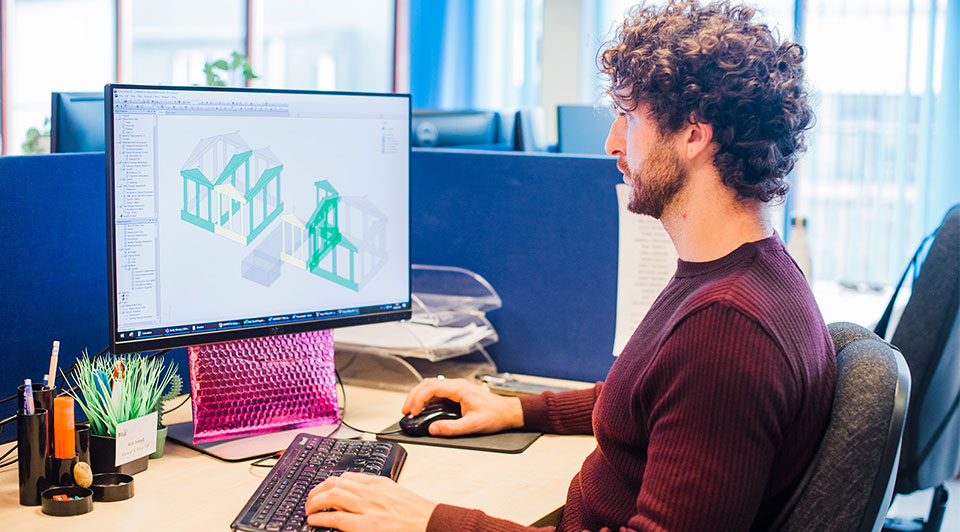
Contamination
How come you missed the contamination?
Occasionally, unexpected contamination is found, beneath buildings or slabs not previously accessed or in the ground between trial pits where no source was identified for its presence.
This can be dealt with fairly easily. Discuss the occurrence with your engineer and we can visit, assess the issue, and provide advice on dealing with it. This can be done without it becoming a big problem causing delays.

Ground-gas
Do I need ground-gas monitoring if I have deep Made Ground, Alluvium, or a backfilled gravel pit nearby?
If I have CO2 over 5% or CH4 over 1% in my monitoring data, does that mean membranes and gas protection?
Is it easier just to install a membrane?

Delays caused by site issues
Concrete and hardstanding breaking out is delaying our SI. What should we do?
Why is my report taking so long?
And getting it right is in all our best interests.
Why do you have to repeat the soakage tests?
Why is the regulator questioning the borehole locations sunk during the previous Site Investigation?
Dense ground has resulted in our application being refused. Why?

Verification
Do I need someone to independently test my imported Topsoil?
What about muckaway and WRAS?
Determining appropriate water supply connection pipe materials is a small, but still important aspect of SI. The possibility that hydrocarbons can leach through plastic pipes and impact water supply, is an important consideration in brownfield development, which is sometimes overlooked.
The WRAS requirements look at levels of hydrocarbons, such as PAH’s and TPH’s (plus VOC’s and other compounds should the Desk Study suggest their presence) at the proposed depth of pipe laying and deepening on the results suggest the correct pipe materials for the site. We assume that you do not want to be laying expensive barrier pipe when you do not need too.

Drainage
Do I need BRE365 compliant tests to aid my drainage design?
Technically, and in most circumstances, yes! Some people will do what is called a BRE365 equivalent test, which is basically the same as a pV test for a drainage field (treated foul). The trouble with this is the holes that pV tests are undertaken in are too small to comply with BRE365 (1m long and 0.30m wide). So, such tests can only provide an indication, alongside tests like falling head tests in boreholes and it may well be, the council drainage officers will ask for full compliance on checking.
Can you complete a BRE365 test in a day?
Is there much point in carrying on past a day?
Do I need to confirm overwinter groundwater levels to supplement SUDS design?
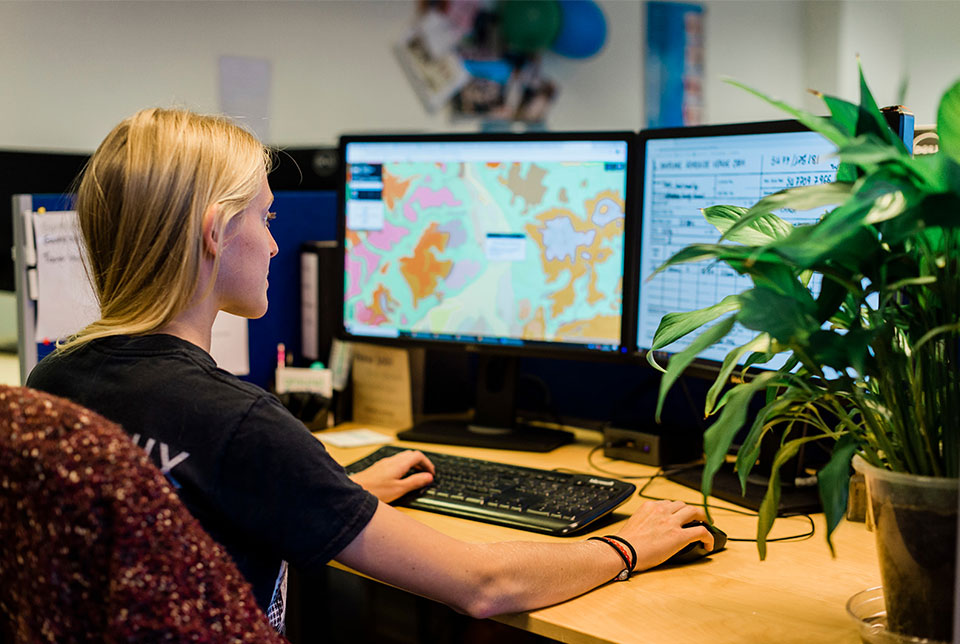
General problems
What other issues could cause problems and add cost?
Sometimes it is just the simple things: Like digging a trial hole to a depth of 2.5/3m, directly in line with a proposed foundation trench. It creates disturbed soils to depth on a foundation line, which have to be dug out at a later date.
Is hidden shallow groundwater an issue?
You have highlighted chalk dissolution as a risk, really?
Yes, chalk dissolution can cause significant issues with respect to getting out of the ground and drainage design, so should not be taken lightly. But it’s a matter of risk assessment and mitigation. It can be assumed to be present and mitigated against, or fully investigated depending on the risk, rather than just referencing the BGS ground dissolution maps. We will discuss this with you every step of the way and make sure you are building and out of the ground in the most cost-effective way possible.
Do we need a CBR test?

Aftercare
Can I talk to you about the report so I can fully understand its conclusions?

Geoenvironmental
Geotechnical
Who We Are